Automated Inspection reduce hazardous landfill by 20%
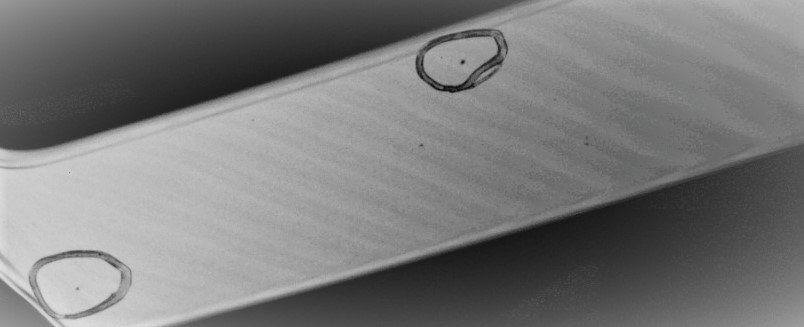
Reflective surface quality
Reflective surface quality is typically only a visual factor and has little to do with any functionality of the product. Hexagon has developed the CSD® (Covered Stereo Deflectometry)® technology to automatically inspect the visual quality of high gloss surfaces. CSD® is a 3D-technology and it works regardless of the part shape. We like glitter and curvy shapes!
This post is about how automated inspection changes the game in terms of reducing waste which is hazardous and non-recyclable. It goes to landfill and often includes plastics and metals containing chemical substances.
This significant change is regardless of whether you have a chrome-plating, painting or PVD coating line. All these methods have their own delicate production processes and thus the product flow and handling in the factory varies; nevertheless, the quality requirements are high, especially in the automotive industry. High gloss surface parts are usually decorative, which means that they create a certain look and feel for the end user. It is understandable that OEMs want to have a perfect surface especially in areas which are always visible. The visual effect often includes lights to amplify the look and feel; this again intensifies the required level of surface quality and forces the parts suppliers to inspect all products they deliver.
The variation in Manual inspection
Because of the tight criteria, the suppliers in all tier levels are making a careful inspection of the parts they deliver. The most difficult surfaces to inspect manually are the high gloss surfaces. These high gloss surfaces are often used in the interior design of the cars.
The downside of the good-looking interiors is that the output from manual inspection is an unknown variable. This means that during the day the repeatability and the performance overall changes constantly. This happens between inspectors, and with the same inspector who gets different results for the same part when repeating the task. Everyone in the field knows very well that people are not good at this task. We tend to fail relatively often and even more, it is difficult for us to keep our performance consistent over days and weeks.
Our customers have reported 80% accuracy on average per inspector.
Hexagon CSD® has achieved 99.97% accuracy in sorting.
I do not judge or criticize the inspectors – it is a really difficult task given the crazily tight criteria demanded by the cycle time. People are hired to find defective parts. Naturally everyone performs their job as best they can. Also, what is a bigger mistake – to let a defective part go to the customer and get a claim handling case as a result, or to scrap some part just for the sake of being sure?
Yes, because of the mindset, no matter how well people are trained, they will send OK parts to landfill due to scrapping them. After all, they do their job well when they see a defect and reject that part. Try it yourself, with whatever item you have on your desk; put a timer on, pick up the part, look at all sides of it and try to find a 0.2mm2 defect, then put the item back in the same place, or somewhere else if there was a defect. You have six seconds to complete the task. Repeat that inspection process for 30 minutes. In that 30 minutes you should be able to handle 300 parts! Can you maintain that pace and find all the defects? Let´s add some difficulty, so find a mirror-like glossy surface part, make sure you are looking at it in very bright light and try to find the defects on the surface. Keep in mind that chrome-plated plastic is not recyclable in an economic way.
Compare the numbers between automated and manual inspection
Automated inspection is typically faster, and always more accurate than manual. Hexagon CSD® has achieved 99.97% accuracy in sorting – that is 300ppm. Again, this number comes from our customers. What is the effect in terms of waste? Let´s put the numbers around the problem using only interior door handles as an example. The industry produces roughly 100 million cars this year – which equals roughly 350 million door handles.
Assuming 6/10 times when people make a mistake in sorting, they scrap an OK part and the remaining 4/10 times is the other way around, that is a NOK part going into delivery. Again, these are numbers confirmed by our customers, but we have rounded them down to be a little more conservative than real life, thus being kind to the manual inspectors. So, 80% sorting accuracy results in 70 million mistakes made in manual sorting annually. Automation would handle these cases according to criteria. So, 60% of that 70 million is OK parts in scrap, and 40% is NOK parts in delivery. Implementing automation enables 20% less waste. One interior door handle has a mass of 100g, therefore the total reduced waste is 1400 tons.
And that is only in door handles hazardous waste, going into landfill…
Luckily, there are different solutions available today.
To learn more about CSD® technology and automated inspection of highly reflective products, please contact us.
We look forward to discussing the subject with you further!
Follow us on social media